Innovative HRSG Cleaning could save you $600,000 or more per year
NEWS
BLOG
EPIC
HRSG CLEANING
HEAT RECOVERY STEAM GENERATOR
TANK CLEANING
INDUSTRIAL TANKS
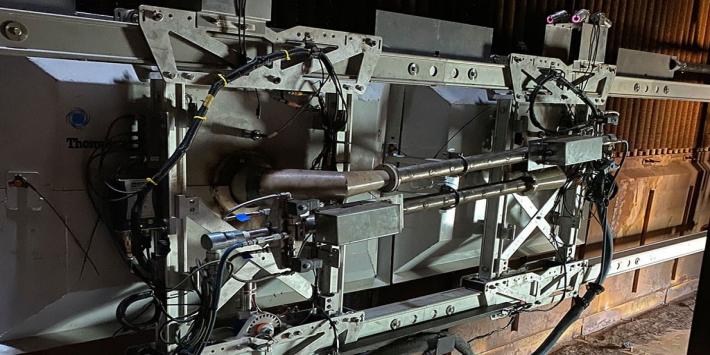
Heat recovery steam generator cleaning, also known as HRSG cleaning, is a common process that significantly increases efficiency and cuts down costs. Avoiding proper HRSG maintenance could cause significant damage and loss of time when trying to operate smoothly and efficiently.
What is HRSG Cleaning?
Proper HRSG cleaning is an efficient way to gain back lost performance because it reduces the back-pressure on the gas turbine, allowing greater net power output as well as reducing cost of fuel per megawatt generation.
Depending on the price of fuel, an additional half inch (water column) of pressure drop through a typical F-class HRSG reduces the bottom line by around $100,000 per year. At least 3-6 inches of pressure loss could be restored with a cleaning on a fouled HRSG.
Negative Effects from Neglecting HRSG Systems
If HRSG tubes are not properly cleaned, this could compromise plant performance in several ways. A plant's heat rate increases, therefore reducing the heat transfer and increasing the back-pressure of the gas turbine whenever there is consistent contamination of the gas-side HRSG tubes.
The output of the steam turbine is also compromised whenever there is reduced heat transfer due to fouled HRSGs and excessively fouled HRSGs can exceed their designated back-pressure limit, triggering an expensive and automatic "turbine trip" or curtail otherwise available generation capacity.
Types of HRSG Cleaning Methods
It's critical to consider what cleaning procedures have previously been accessible and what drawbacks and risks exist with them. Dry ice blasting, for example, is a common off-line cleaning technique that necessitates scaffolding or "sky climbers" and is expensive, time-consuming, and ineffective due to factors like below-360-degree coverage, limited penetration of multiple harps, and an incomplete cleaning of the densely contaminated finned tube bundles.
Another option is to use a bag-exploding technique that involves dangling bags of combustible gas at various elevations and detonating them in open spaces between bundles. This may be costly, time-consuming, and result in unwarranted, random impact on surfaces, expansion joints, instrumentation, equipment, and structural components.
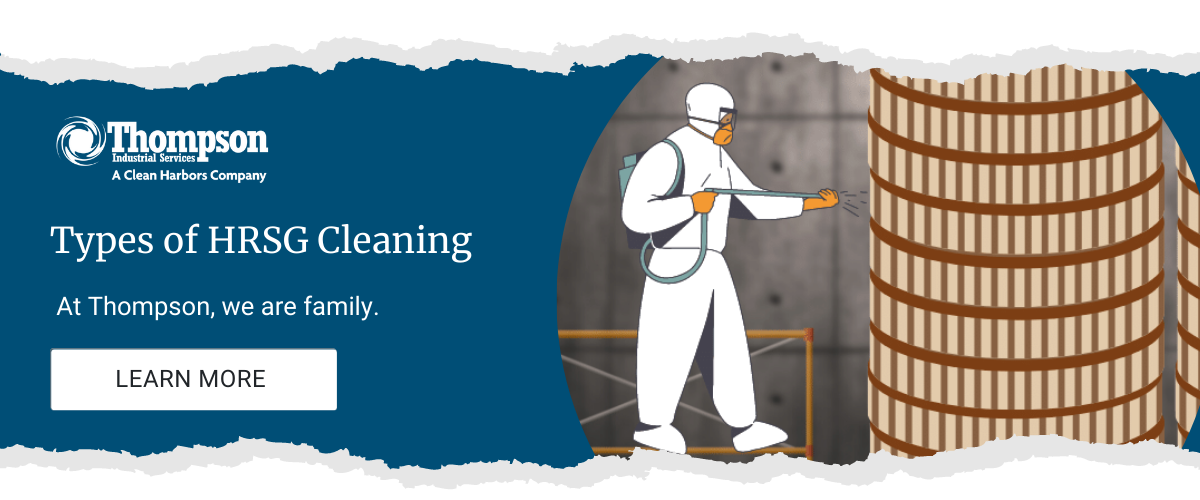
EPIC Off-Line HRSG Cleaning
Fortunately, 14 years of proven technology have been incorporated into a fresh solution. EPIC off-line HRSG cleaning safely provides highly beneficial results to combined-cycle plants without unwarranted explosive effects.
In comparison to other existing methods, the off-line application of this substantiated pulse-detonation cleaning technology, utilized routinely on-line for continuous, around-the-clock performance for well over a decade, has demonstrated dramatic improvements in highly contaminated, tightly packed finned harps in HRSGs when compared to existing methods.
Benefits of EPIC "Shockwave" HRSG Cleaning
- Effective: Over the past 14 years, shockwave cleaning has unfailingly provided penetrating, all-encompassing cleaning energy that can extend far into the tube bank and effectively dislodge deep and impacted deposits from heat-transfer surfaces.
- Convenient: With this advanced technology, an automated cleaning rig that can navigate quickly across the heat-transfer surface without the need for scaffolding or man-baskets is employed. This significantly reduces overall cleaning time in comparison to other methods.
- Safe:The shockwave cleaning energy is remotely activated and concentrated safely within the 2-inch combustion tube, which is specifically designed and patented. It's then vented straight away and focused exclusively on the heat-transfer surface, avoiding harm to surrounding structures from uncontrolled and potentially fatal explosions.
Fouling on the gas side of HRSG tubes compromises plant performance. Lost performance may be restored through innovative HRSG cleaning, which reduces back-pressure on the gas turbine, increasing net power output. Through this method, combined-cycle facilities are regaining 3-6 inches of pressure drop and increasing their bottom line by $600,000 or more annually through reduced fuel costs.
Off-line pulse-detonation cleaning technology from EPIC reduces hazard exposure, cleaning time, and outage duration when compared to other HRSG cleaning technologies. When it comes to safety concerns of various HRSG cleaning techniques, EPIC's off-line pulse-detonation technology minimizes risk.
Why Choose Thompson for your HRSG Cleaning?
Are you in search of industrial HRSG cleaning, maintenance and services?
Thompson Industrial can help maximize your HRSG's efficiency and performance while cutting your operating costs!
Contact us today!
Original article from BIC Magazine