Types of Heat Recovery Steam Generator (HRSG) Cleaning
NEWS
BLOG
EPIC
HRSG CLEANING
HEAT RECOVERY STEAM GENERATOR
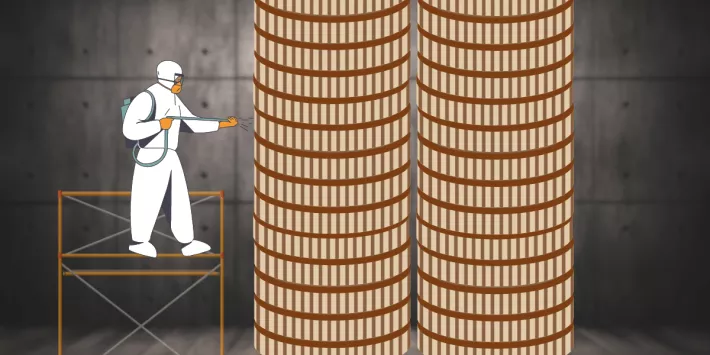
Heat Recovery Steam Generators (HRSGs) are the linchpins of energy optimization in industrial settings. Their performance, however, can decline due to debris accumulation on their heat-conducting finned tubes. Ensuring their cleanliness is crucial for sustaining efficiency, safety, and cost-effectiveness.
In this guide, we’ll explore the varied HRSG cleaning methods, focusing on cutting-edge and eco-friendly options. Whether you're a plant manager or an industrial maintenance specialist, this comprehensive insight will arm you with the know-how to make judicious decisions regarding HRSG maintenance.
In a thermal oxidizer, gas turbines, or other heat generating processes, energy is lost. In order to recover the energy, we produce steam using Heat Recovery Steam Generators (HRSG) so it may be used for other purposes.
You will find that HRSG systems are used in a variety of commercial and industrial applications. Most commonly, HRSG systems are used for large energy projects, cycle power plants and even large universities. Recovering energy allows schools to provide power to their campus, can heat spaces or provide hot water to residences.
What is HRSG Cleaning?
Over time, a Heat Recovery Steam Generator (HRSG) will accumulate debris and build up deposits on their finned tubes. Because the finned tubes are used to conduct heat, the deposits that gather cause a resistance when trying to transfer heat through the fins and slows the turbine.
The debris and contaminant build up on a Heat Recovery Steam Generator (HRSG) can be detrimental to efficiency, cost, and overall performance. This makes HRSG cleaning and maintenance, repairs, servicing and inspections an important strategy to ensure efficiency for fixed facility plant owners, safety for plant personnel, and mitigate financial loss.
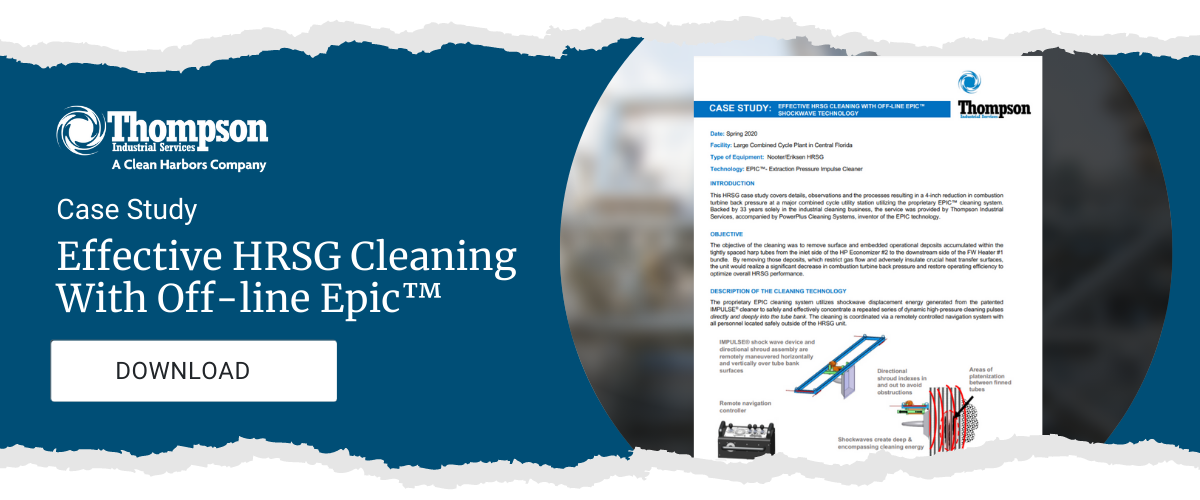
Types of HRSG Cleaning
The most prevalent types of cleaning technology on the market include high-pressure water blasting, grit blasting, carbon dioxide (dry ice) blasting, and pressure wave cleaning. Each has its own set of advantages, so a plant's choice is determined on a case-by-case basis.
- Pressure Wave Cleaning
- High Pressure Water Blasting
- Grit Blasting
- Dry Ice Blasting
Pressure Wave Cleaning
Pressure wave cleaning involves feeding a hose into a heat recovery steam generator. As it maneuvers around the inside of the system, the engineer uses a computer to control the ethane-oxygen gas that is released inside. This gas causes pressure waves to rattle the contaminants inside of the HRSG, dislodging the debris. It then settles to the bottom of the HRSG, making it easier for cleaning.
The EPIC™ pressure wave system was designed to improve current HRSG cleaning methods and do so safely and quite effectively without damage or stretching to any combined cycle components.
Although various HRSG cleaning systems exist, none can now reach the same standards and controls set by EPIC. This proprietary technology removes deposits that have built up and are lodged deep into the harp’s finned tube bundles.
High Pressure Water Blasting
High pressure water blasting (also known as hydrojetting or high pressure cleaning) sends high-speed, pulsating water that is generated by a water jet to remove surface material and contaminants.
The energy generated from ultra-high pressure hydroblasting exceeds the bonding of even the most adherent coatings or process contamination. The usage of high pressure hydroblasting equipment is not only highly efficient in a variety of sectors, but it is also environmentally friendly, lowering carbon emissions.
Grit Blasting
Commonly known as sandblasting, abrasive grit blasting forcibly propels an abrasive media (material) using pressurized water, steam or compressed air. The blasting material smooths rough surfaces, can roughen smooth surfaces, shape a surface or remove surface contaminants.
The blasting process can involve using different media; some being highly abrasive and other having a mild effect. A huge number of factors influence the selection of media. Many times, it is necessary for an engineer to complete sample processing to take place before the final media type, size, and equipment is chosen for the grit blasting process.
Common abrasives used include:
- Steel grit
- Crushed glass
- Aluminum oxide
- Plastic
- Baking soda
CO2 (Dry Ice) Blasting
For several reasons, dry ice blasting is commonly recognized as one of the best techniques for cleaning HRSG's. In most cases, sand blasting and high-pressure water blasting result in a secondary waste stream, contributing to the amount of waste.
Having to cleanup more waste increases the overall cost and time of a project. Dry ice blasting does not promote corrosion and abrasion, is FDA approved and is an environmentally safe process. Because CO23 blasting doesn't involve using abrasives or excessive water, no secondary waste is produced. This not only minimizes the cost, but also reduces the process's completion time.
Why is HRSG Cleaning Important?
Heat Recovery Steam Generators (HRSGs) play a pivotal role in harnessing waste heat from exhaust gases and converting it into usable energy. Given the vital role they play, it’s imperative to keep them operating at optimal levels. HRSG cleaning is not just a routine maintenance activity; it is an essential element in ensuring efficiency, prolonging the lifespan, and promoting the safe operation of these systems. Here's why HRSG cleaning is so critical:
1. Maintaining Efficiency
Over time, HRSG finned tubes can accumulate debris, dust, and other particulates. These deposits act as an insulating layer on the heat transfer surfaces, impeding the efficient transfer of heat. This impedance means that the HRSG has to work harder to extract the same amount of energy, leading to increased fuel consumption and reduced efficiency. Regular cleaning removes these deposits and restores the HRSG's ability to transfer heat effectively.
2. Prolonging Lifespan
The build-up of deposits can also contribute to corrosion and physical stress on the HRSG components. For instance, fouling can lead to hotspots on the tubes, which in turn can cause tube failures over time. By regularly cleaning the HRSG, you’re not just removing the deposits but also mitigating the risks associated with corrosion and stress, which can significantly extend the lifespan of the unit.
3. Preventing Costly Breakdowns
An HRSG that hasn’t been properly maintained is more likely to experience breakdowns. These breakdowns can be catastrophic, requiring extensive repairs or even full replacement of the unit. Such breakdowns are not only costly in terms of repair but can also lead to significant downtime, affecting the plant’s production and revenue. Regular cleaning is a preventative measure that helps avoid these costly breakdowns.
4. Ensuring Safe Operation
Deposits and debris build-up can also create safety hazards. For example, excessive deposits can lead to overheating, which in severe cases can cause fires or explosions. Additionally, blocked or fouled tubes can lead to increased pressure within the HRSG, which poses additional risks. Ensuring that the HRSG is clean and free of deposits is paramount in maintaining a safe operating environment.
5. Environmental Compliance and ESG Considerations
HRSGs are often subject to stringent environmental regulations regarding emissions and efficiency. A dirty HRSG is less efficient and may produce emissions that exceed regulatory limits. Regular cleaning ensures that the unit operates within the mandated regulations, helping to avoid fines and reputational damage.
Moreover, in the context of Environmental, Social, and Governance (ESG) considerations, maintaining HRSGs in an eco-friendly manner has become more critical than ever. ESG criteria are increasingly being used by investors and stakeholders to evaluate a company's practices and their impact on the environment and society.
6. Predictive Maintenance and Inspection
Clean HRSGs are easier to inspect and monitor. When the surfaces are free of deposits, it's easier to conduct non-destructive testing and other inspection methods that can predict and prevent future problems. This aspect of cleaning can help in planning maintenance activities more efficiently.
Looking for HRSG Cleaning?
Are you in search of industrial HRSG cleaning, maintenance and services? When your plant’s HRSG unit is effectively cleaned, it will restore performance that was previously lost because insulating deposits.
Thompson Industrial can help maximize your HRSG's efficiency and performance while cutting your operating costs!
Contact us today!
Related Articles
Thompson Industrial: Your Chemical Cleaning Expert - When you need industrial cleaning services, there is no better option than Thompson Industrial Services.