Winning in Safety for Industrial Services When the Pressure Is On
BLOG
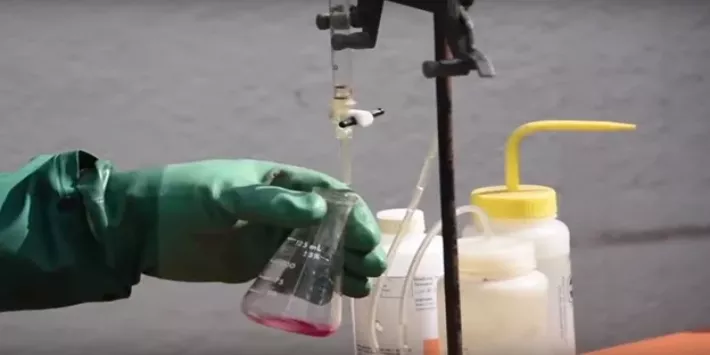
It happens more often than you would think: a team of technicians from Thompson Industrial Services arrives at a customer’s site to perform a cleaning task and finds that the equipment in question has gone many years, sometimes even decades, without a complete cleaning. Usually, this is because the equipment was built and installed without carefully considering the logistics of performing maintenance on it down the road. Other times, the environment surrounding the equipment has changed in a way that makes it difficult to access, or the equipment itself has changed slightly over the years, making it hard to clean with traditional methods. Recently, our cleaning teams worked together to devise a creative solution for cleaning an unusual type of heat exchanger tubes. Here’s the story of how we came through for our client and solved a years-old efficiency problem. Hydroblasting Limitations The equipment that our team needed to clean was a bundle of heat exchanger tubes, which they would normally work on with a hydroblasting system—a long “lance” with a nozzle on the end that sprays high-pressure water and knocks debris loose inside the tubes. But this particular bundle was a U-shaped, or “hairpin” design, meaning that the tubes make a sharp 180-degree bend partway down their length. This bend does not allow a nozzle to pass through, which means that a standard hydroblasting cleaning will always leave some amount of debris in that area of the tubes. This highly specific problem is a well-known challenge in the industry, but our experienced technicians came up with a suggestion for the client that they thought would solve it for them. Chemical Cleaning Alternatives Our team recommended attacking the debris buildup in the U-shaped bend using chemical cleaning solutions rather than a hydroblasting nozzle. The chemical solution would ideally make contact with all of the debris, dissolving and removing it to leave a completely clean tube interior. The client agreed with the proposal and our team got to work creating just the right chemical solutions for the specific residues and equipment involved.
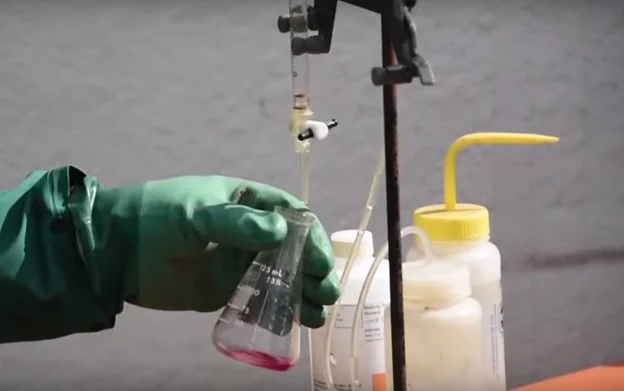
Chemical cleaning is a powerful alternative to hydroblasting in certain contexts.
As they always do, our chemical cleaning division used their knowledge, experience, and absolute commitment to safety to implement a solution that accomplished the goals of the project quickly and completely. By the time our teams left the customer’s site, the complete length of the U-shaped heat exchanger tubes had been cleared of debris and the equipment was ready to go back online. The client had high hopes that the system would enjoy renewed efficiency after Thompson’s cleaning work, and they were certainly not disappointed. Money-Saving Efficiency To explain the key efficiency improvement in the client’s heat exchanger after the cleaning, it is necessary to describe the valve system that the equipment uses to control the flow of media through the heat exchanger tubes. With the debris buildup inside the tubes before the cleaning, the valves had to be open 100% to allow enough media to flow through to cool/heat the equipment to the proper temperature. After our team’s chemical cleaning work, however, the client discovered that having the valve 24% open was sufficient for allowing the same cooling/heating effect. This is a clear indication that media flow through the bundle of tubes was much greater after the cleaning, giving the heat exchanger and the entire production line dramatically improved efficiency and less wear and tear during normal operation. New Solutions All the Time One of the most important benefits that a client gets when they choose to work with Thompson Industrial Services on a difficult industrial equipment problem like this one is our creative, knowledge-driven approach to problems. If a certain maintenance task has never had a satisfactory solution, our teams are not content to simply follow the standard protocol, leaving the problem partially unsolved. Our technicians and project managers use Thompson’s resources of customizable equipment and deep knowledge of the field in order to devise solid ideas for finally resolving those tough cleaning problems. Email us today to discuss the maintenance issues that have created problems for your facility for years. Our project coordinators are ready to assess those problems and propose solutions to solve them safely, quickly, and cost-effectively.
Back
Press Contact
- Emily Martin
- Marketing Manager
- 100 N. Main Street
- Sumter, SC 29150
- (803) 773-8005
- emartin@thompsonind.com