Three Highlights of a Recent Boiler Tube Cleaning
BLOG
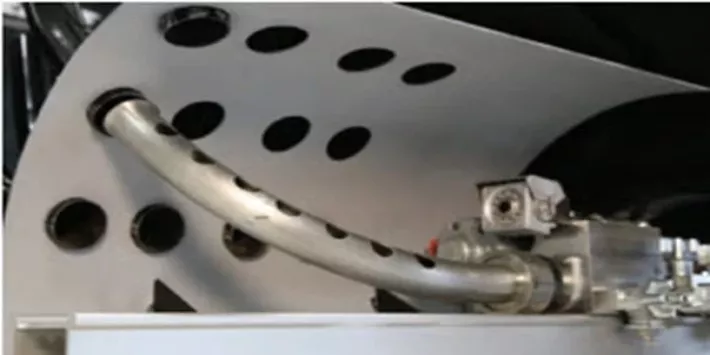
Last month, we got to do one of our favorite things here at Thompson Industrial Services: we served a new customer with our automated industrial cleaning technology. The reason it’s one of our favorite activities is because whenever we meet someone new and perform a cleaning task for them, the client is amazed at the enormous advantages that our systems provide over past cleanings. This project in particular was a prime example of solving a difficult problem that a facility had struggled with for many years, saving them significant amounts of money and excelling in three key areas: safety, productivity, and the client’s bottom line. Boiler Tube Cleaning Our client was a facility here in the southeastern United States, which was looking for a better way to clean a hard-to-reach set of boiler tubes. In the past, the boiler tubes had been cleaned using a two-man team. One technician manipulated a hand lance while positioned inside a very small steam drum, while another technician outside the drum used a foot pedal to control the water flow to the lance. No matter how this approach was executed, it posed serious safety hazards to the technicians involved. Due to these safety concerns, the equipment had not benefited from a cleaning in several years. Safety This type of confined entry challenge is exactly what our automated systems were designed to solve. Rather than placing a technician inside the steam drum to reach the boiler tubes with a hand lance, our team set up a customized automated positioning system, armed with powerful hydroblasting equipment. The technicians controlled the system remotely with specialized software, observing the cleaning process on a video screen. No technician had to enter a confined space at all, and the hydroblasters were kept at a safe distance from all employees.
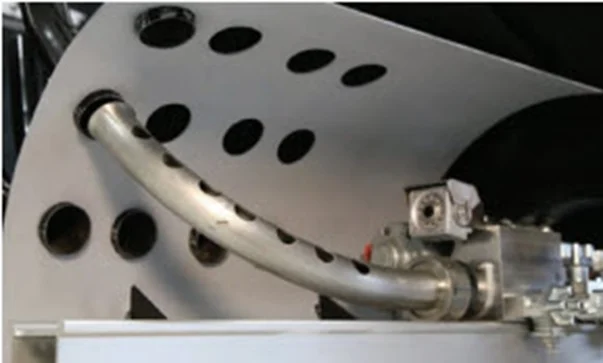
Our advanced camera system helps with boiler tube cleaning accuracy.
Productivity While safety is the top benefit of mounting hydroblasters on automated positioners rather than handling them manually, it is certainly not the only one. Our robotic equipment does not get tired out like a human technician does, so there is no need for breaks. And because the equipment can move at a constant rate, the resulting cleaning is extremely uniform and thorough. By keeping an eye on the hydroblasting progress on the remote video screen, our experts are able to focus on using the powerful equipment to its full potential, rather than being distracted by confined-entry safety protocols and human error while handling a hand lance. Bottom Line When a service enhances both the safety and the productivity of a very difficult industrial cleaning task, the inevitable end result is a very welcome change to the client’s bottom line. At the end of this job, it was concluded that the entire boiler tube cleaning process was 12 hours shorter than it had been for previous cleanings. That time translated directly into $6,000 worth of savings for the client, a difference that any facility manager would be quite pleased with! As robotic, remotely controlled equipment expands into more and more areas of our industry, a cleaning task like boiler tube cleaning is an ideal application for this exciting new technology. There is no longer a need to risk the safety of technicians by placing them in confined spaces with powerful hydroblasting or chemical cleaning tools when an automated piece of machinery can perform the same task more safely, more quickly, and more thoroughly. Thompson Industrial Services Teams from Thompson Industrial Services use automated positioning equipment to perform many other difficult cleaning tasks as well, with equally impressive results. Stripping mineral scale and other types of debris from the interior of large vessels, for instance, no longer requires lowering a human technician inside. By using an automated system to manipulate multiple hydroblasters at once, our teams can often clean these pieces of equipment without even taking them offline. To learn more about the wide range of potential applications for our fully customizable automated systems, visit the service pages on our website. You’ll find more success stories as well as demo videos showing our remotely controlled hydroblasting, hydro-cutting, chemical cleaning, and proprietary FINFOAM equipment in action. Our teams look forward to solving your toughest industrial service challenges.
Back
Press Contact
- Emily Martin
- Marketing Manager
- 100 N. Main Street
- Sumter, SC 29150
- (803) 773-8005
- emartin@thompsonind.com