The Science Behind High Pressure Water Jet Cleaning
BLOG
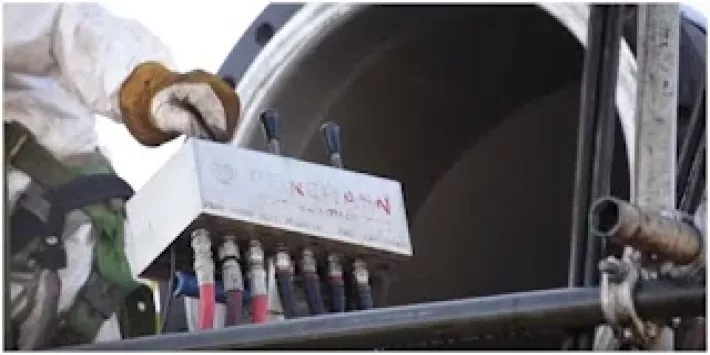
The concept of water blast cleaning is foundational to many of our most popular, effective, and money-saving services. No one is surprised by the general idea of water cleaning equipment and surfaces, but there are many types of debris and deposits that we assume would take something other than plain H2O to remove. As the clients of Thompson Industrial Services discover on a regular basis, however, in the right hands water blast cleaning becomes one of the very best options for removing the toughest deposits, coatings, and debris that an industrial facility has to deal with. Our post today takes a look at the special tools and methods that harness the power of high pressure water blasting for a wide range of different industrial cleaning tasks.
Pressure
Successfully accomplishing the most difficult cleaning tasks—operations like stripping away multiple layers of old paint or non-slip floor coatings, for instance—calls for incredible water pressure. Our specialized equipment is capable of delivering up to 40,000 PSI of water pressure. By way of comparison, a standard “medium duty” pressure washer that you might use around the house for washing mildew off vinyl siding, cleaning the driveway, etc. packs between 2,000 and 3,000 PSI. Even heavy duty commercial pressure washers for cleaning concrete or stripping paint don’t typically go above 5,000 PSI. At eight times that level of power, our 40,000 PSI water blast cleaning solutions give our technicians the power to clear debris of types that the average homeowner will never see!
The flip side, of course, is that handling ultra-highpressure water blasting equipment can be very hazardous for workers, equipment, and surfaces in the area. Historically, our technicians at Thompson Industrial Services have minimized the risk by using protective clothing, gloves, and other equipment, undergoing extensive hands-on training, and adhering to our strict internal safety procedures. At the same time, however, our progress in automation technology is gradually taking water blast cleaning equipment out of the hands of our workers altogether.
Our automated equipment keeps our workers at a safe distance while providing superior cleaning.
The safest way to use water blasting equipment with up to 40,000 PSI of water pressure is by manipulating it with robotic tooling. For many years, our engineers have been steadily researching, testing, and implementing methods for hydroblasting that keep our workers at a safe distance while machines do the “heavy lifting.” While there are a wide variety of specific applications, in most cases our teams set up the system with the appropriate water blast cleaning tools, connected with robotic tools that manipulate the hydroblasters, and sometimes control the system remotely with the help of customized software on tablet devices.
Not only is this approach vastly safer than previous manual cleaning methods, but it also outperforms them in terms of efficiency. Human technicians are restricted in how quickly they can work, and even the most seasoned technicians occasionally make mistakes. With safety protocols in place, those mistakes may not lead to injury or damage, but they may leave some debris behind, which will continue to reduce the efficiency of the partially cleaned equipment. Automated hydroblasting equipment can do the same job far more quickly than a human technician, partly because there are fewer safety precautions to follow at the work site and partly because it can handle multiple cleaning tools at the same time. Our remote control software also helps us ensure complete cleaning, especially with complex equipment such as bundles of boiler tubes.
Cost-Effectiveness
The increased speed of an automated water blast cleaning compared with a manual one means that the same maintenance job costs our client less in terms of money and downtime. It also provides the client with a more thorough cleaning than a human technician could accomplish, which sets the line or facility up for more efficient production and less equipment wear and tear until the next regularly scheduled servicing.Never content with the “status quo,” our project managers continually look for creative ways that they can cut downtime even further for our clients. They come to each new job with a fresh thought process, assessing the client’s equipment and cleaning needs and determining which of our efficient, affordable water blast cleaning systems is exactly right for that specific task.
Press Contact
- Emily Martin
- Marketing Manager
- 100 N. Main Street
- Sumter, SC 29150
- (803) 773-8005
- emartin@thompsonind.com