Case Study | Extraction Pressure Impulse Cleaner
NEWS
BLOG
EPIC
HRSG CLEANING
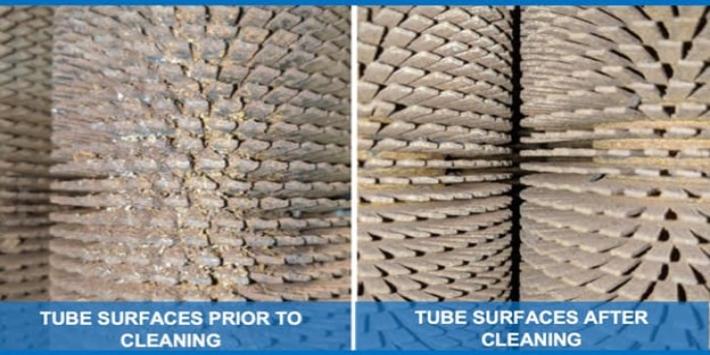
This HRSG cleaning case study covers the processes and results of a 4-inch reduction in combustion turbine back pressure at a major combined cycle utility station utilizing the proprietary EPIC™ (Extraction Pressure Impulse Cleaner) automated cleaning system.
Overview
The EPIC™ (Extraction Pressure Impulse Cleaner) cleaning system effectively dislodged and removed the deep and heavily impacted deposits that had accumulated on and within the finned tube surfaces of the HRSG. The service required five (5) day-shifts of operation with a singular crew. This included setup and dismantling with coordinated off-shift vacuuming by Thompson’s own personnel and equipment to remove the considerable amount of dislodged debris.
Problem
A large combined cycle utility plant was experiencing substantially reduced efficiency and performance from their HRSG industrial boilers. This was due to the insulating and CT back pressure effects from excessive deposits on and deep within the finned tube bundles. Prior cleanings performed, typically every other year, had not been sufficiently effective.
Solution
The plant researched multiple options to achieve a more effective and penetrating means to clean all their bundles downstream of the SCR. After completing their research, the plant selected the patented EPIC™ technology that safely utilizes a series of repeated and concentrated dynamic shockwave cleaning impulses (IMPULSE® pressure waves) directly and deeply into the tube bank. The cleaning is coordinated using a remotely controlled navigation system with all personnel located safely outside of the HRSG cleaning unit.
Results
The post-cleaning visual inspection, complimented by video using a borescope, provided empirical evidence of the Extraction Pressure Impulse Cleaner's effectiveness. The operating performance was later tabulated and evaluated by plant engineering and management personnel, resulting in comments such as one from the Operations Manager being “thrilled” with the results and the Plant Manager enthusiastically stating
“EPIC is the way to go to clean our HRSGs and we’ll use it again in the spring for our next one.”
Based on a 6-month comparative operating data that was voluntarily shared with Thompson, it was determined that
the combustion turbine back pressure was reduced by 4 inches of water column, resulting in a heat rate
decrease by roughly 0.5 MMBtu/MWh. This was computed to yield an equivalent payback in 1,018 hours (41
days) due to reduced fuel costs, based on a 100% production (MW) load.
Benefits
The proprietary EPIC™ (Extraction Pressure Impulse Cleaner) cleaning system utilizes shockwave displacement energy generated from the patented IMPULSE® cleaner. The IMPULSE® cleaner safely and effectively concentrate a repeated series of dynamic high-pressure waves directly and deeply into the tube bank. The cleaning is coordinated via a remotely controlled navigation system with all personnel located safely outside of the HRSG cleaning unit.
The automated and remotely operated EPIC™ cleaning system is extremely safe for personnel as well as the entire HRSG structure with numerous fail-safe features fully integrated into the overall process. Other unique high-tech
features of the EPIC™ process include:
- Real time observation of the cleaning progression from 6 system cameras monitored within the ground level command center on a large screen display.
- Progressive back pressure reduction of each segment, as it's being cleaned, is also captured and trended in the control module.