A Major Piping Hydroblast Solution
BLOG
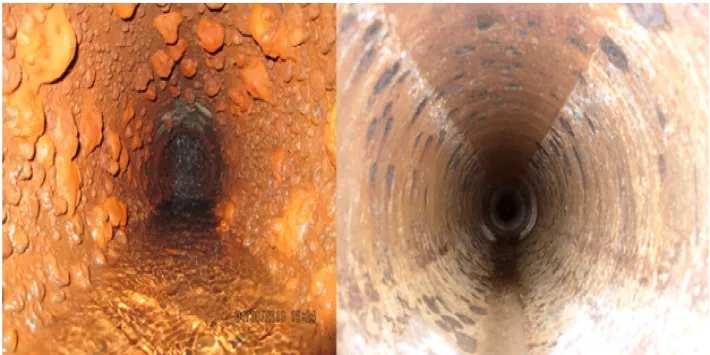
Hydroblasting to clean piping of all types and diameters has been a core competency for Thompson Industrial Services for many years. Recently, we accomplished yet another successful hydroblast project for one of our long-standing clients, and the job exemplifies the way this approach outperforms alternative cleaning methods in a variety of important areas. Here’s a brief look at the work we did for this client to solve their piping issues at a facility where contamination of the surrounding area had to be avoided at all costs. Essential Services Affected The project was located at a nuclear power plant, where a fire protection system was being negatively affected by large amounts of corrosion in its water piping (See “before and after” photos below). Removing this corrosion was critical in order to restore adequate water flow through the piping in the case of a fire emergency at the plant. Due to the plant’s safety protocols, the waste material could not be allowed to contaminate the surrounding area during the cleaning process, so one of the requirements for our hydroblasting team would be to collect, contain, and remove from the site all of the residue and cleaning substances used in the job. Alternative Cleaning Methods Hydroblasting was not the only possible option for clearing the corrosion from the piping interior. Mechanical and chemical cleaning methods were also available, but it was determined that each of these strategies would have incurred more cost than the hydroblasting option. The other possible solution, removing the corroded piping completely and replacing it with new infrastructure, would have been a far more expensive, lengthy, and disruptive process. The client agreed with our experts’ recommendation to clear the piping using Thompson Industrial Services’ powerful, versatile hydroblasting equipment, following a careful analysis of the nature of the corrosion and selection of exactly the right nozzles, water pressure, and other details for the project.
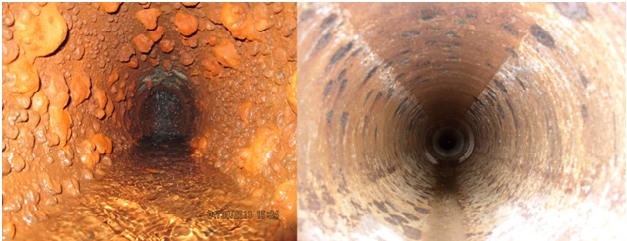
Piping before and after hydroblasting
A Successful Hydroblasting Project Our team decided to use a 12k hydroblast unit with a powerful nozzle specially selected for the pipe’s diameter and the corrosive material. They also employed a centralizer, an attachment to keep the hydroblaster located in the center of the pipe throughout the cleaning process. This ensured an even, complete cleaning in the shortest possible timeframe. Although there was a large amount of waste material that our team had to remove from the piping, they employed our vacuum system to collect the debris as it was loosened from the piping interior. The vacuum system also collected the water used in the hydroblast process, so there was no contamination or moisture introduced to the environment at the nuclear plant. Client Satisfaction Because we had done quite a bit of work for this client in the past, they were already familiar with the high quality of work that Thomson Industrial Services brings to every job. The client did note, however, in a letter sent to us after the project’s completion that they appreciated the flexibility, proactive attitude, and responsiveness of the entire TIS hydroblasting team. Not only was our team able to clear the piping corrosion very quickly, safely, and cleanly using a tailored hydroblasting solution, but they also exemplified respect for the nuclear plant’s safety protocols, general OSHA standards, and plant management. The client expressed their complete satisfaction with the project and their anticipation of working with our teams in the future for similar industrial services needs. Other Hydroblasting Projects Our research division at Thompson Industrial Services is constantly investigating new ways to improve our hydroblasting efficiency, developing and testing new nozzles and new robotic tools that can help us achieve our goal of 100% automation. Employing these versatile, effective methods at highly sensitive sites such as nuclear power plants, pharmaceutical manufacturers, and other ultra-clean facilities requires a complete understanding of and adherence to safety protocols. In keeping with our company motto to “Be safe, be good, be great,” we take that respect for safety protocols to every single project that we perform for our clients. The result is fantastic relationships with long-standing clients like the one we served in this case, along with many others across the United States and beyond. Browse our website and get in touch with us directly to learn more about our industrial services.
Back
Press Contact
- Emily Martin
- Marketing Manager
- 100 N. Main Street
- Sumter, SC 29150
- (803) 773-8005
- emartin@thompsonind.com