Driving Safety with Data
NEWS
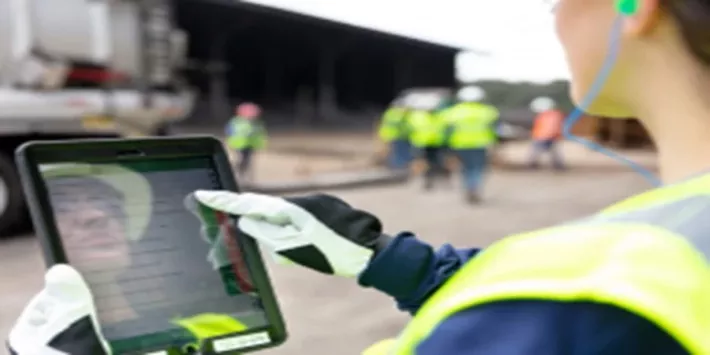
Most industries you can think of have been invaded by a single buzzword: “big data.” In an incredible range of different applications, technology has made it possible for computers to compile, organize, and present huge amounts of information quickly, in turn giving human managers the ability to use that information in unprecedented ways. Here at Thompson Industrial Services, we are very happy about the way big data has benefited one specific, very important area of our business: our safety programs.
Learning From the Past
The particular type of big data that our safety experts use is the collection of records produced during each of our client projects, whether they involve hydro excavation services, automated hydroblasting, chemical cleaning, or one of our other applications. Our automated systems and detailed post-project analytics produce a wealth of valuable information about exactly what happened during the job, and now we have the technological capability to organize that information and use it to make policy decisions about future efforts.
The people that actually look at this compiled data and make conclusions about it come from all divisions of our company. First, each division has its own safety council, which examines its division’s data and responds with its unique level of expertise and knowledge about that particular field. There is also a regional safety council, which takes a broader look at the division councils’ results. Finally, on a quarterly basis our corporate leadership reviews the safety data from across all divisions and regions, providing guidance about what safety policies should be adopted or modified company-wide.
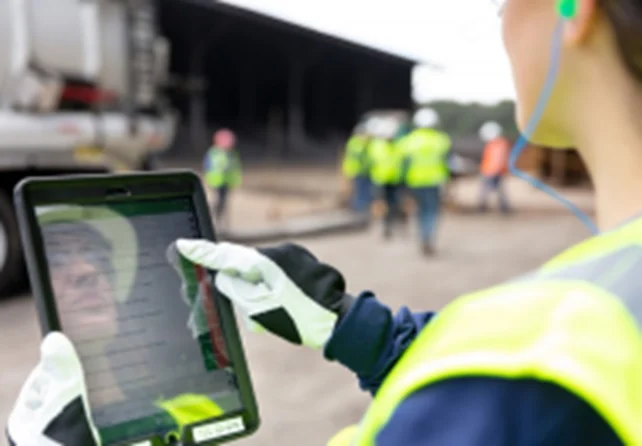
Employees report all relevant safety information through SafetyNet.
Entering the Data
Where does all of this big data come from? We are very happy about the system we have developed at Thompson Industrial Services to keep every field employee, manager, and project coordinator personally involved in improving our safety practices. Each employee has the opportunity to fill out a safety checklist for each hydroblasting or hydro excavation services job, noting any safety concerns, incidents, or other details that have a bearing on future decision making. The division, regional, and corporate safety councils focus on those areas and recommend strategies to mitigate as many of the identified risks as possible.
Layers of Protection
In many instances, the average person’s impression of a safety program is requiring employees to wear hard hats, reflective clothing, safety goggles, and other personal protective equipment. These protocols are standard across our company for any employee who works in the field, but they comprise just the first layer of our SIF prevention program. The second layer includes the standard operating procedures, policies, and training that all of our new employees receive. Before our new employees enter the field and interact with our clients’ equipment, they undergo a stringent training program focused on their specific area of work. The third layer is all about observation: watching what goes on during client projects, identifying any hazards, seeing how our workers perform, and auditing our policies to see if they can be made more effective.
The fourth level is extremely important in our company: automating our processes wherever possible, replacing our technicians with remotely controlled robotic positioners. In this level we also include measures like equipment guards and other safety improvements to the tools that our people use every day.
Finally, at the top level of our SIF prevention program is the removal of hazards wherever possible. If we can substitute a procedure with a safer, equally effective alternative, we do so. If there is a way to eliminate a hazard, we apply the expertise, knowledge, and energy necessary to do so, giving our employees the safest work environments possible.
Be Safe, Be Good, Be Great