Advanced In-Situ SCR Catalyst Cleaning by Thompson Industrial
WHITE PAPERS
IN-SITU SCR CATALYST CLEANING
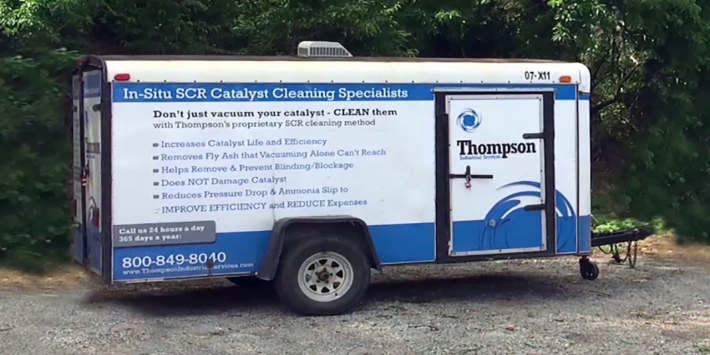
Thompson Industrial Services offers advanced in-situ SCR Catalyst Cleaning Technologies that have been proven to increase efficiency, reduce backpressure, help meet EPA regulations by exposing more catalyst surface area for optimal reaction, and extend catalyst life – all without any damage to the catalyst or modules.
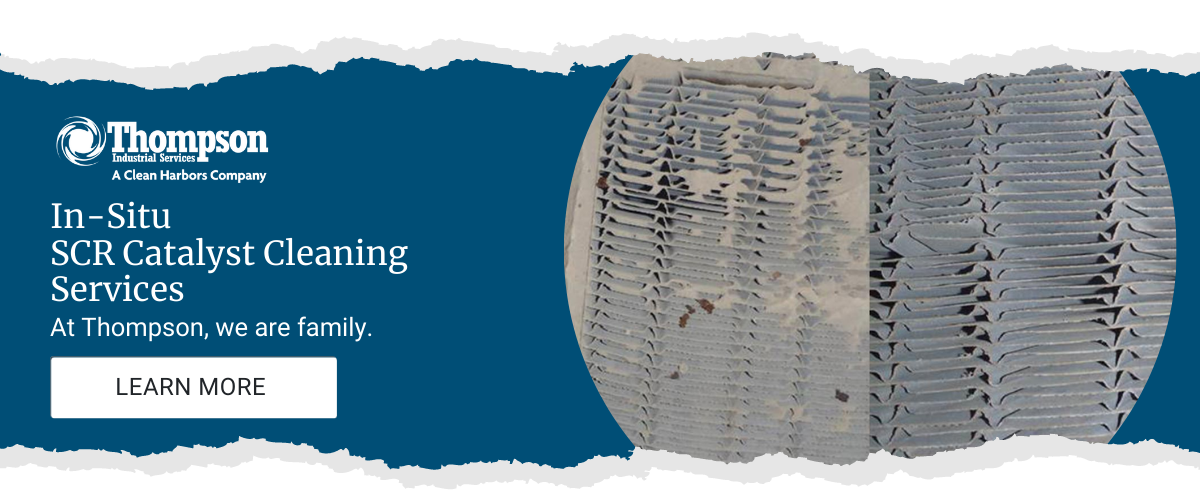
Catalyst Becoming Plugged Can Cause:
- Large and dense ash piles that totally block flow to accumulated areas
- Reduction of surface area for catalytic reaction
- Ammonia to be improperly consumed in the top layer, preventing lower layers from producing oxygen for mercury oxidation and SO2 to SO3 conversion.
- Increase in ammonia slip potential
- Negative effect on reactor flow distribution
- Higher catalyst channel velocity
- Greater potential for catalyst erosion
- Increased backpressure costing for supplemental fan power
SCR for MATS Compliance
With the EPA's MATS requirements, including the oxidation of mercury and the regulation of other acid gases, optimal catalyst performance will become more important than ever for environmental compliance.
Under optimal condition most ammonia can be consumed in the top later, and lower layers can produce oxygen for subsequent mercury oxidation as well as SO2 to SO3 conversion. However, as catalysts become plugged or contaminated, the surface area is reduced. Some of the NOx may not be removed, and the ammonia may not be properly consumed in the top layer. As a result, lower layers may be challenged to produce oxygen for mercury oxidation as well as SO2 to SO3 conversion.
Advanced in-situ SCR Catalyst Cleaning Technologies by Thompson Industrial Services
We offer a solution to safely clear catalysts of potentially harmful contaminants that cannot be reached, dislodged or removed by traditional methods.
Our proprietary method vacuums and blows within a containment from above the catalyst while vibrating the catalyst layers from the bottom, safely cleaning catalysts of potentially harmful contaminants by removing fly ash that cannot be reached by traditional methods. The catalyst does not have to be removed from the unit and the process prolongs catalyst life.
Clears Your Unique Plugging Issue
Whether you are dealing with hardened fly ash, popcorn ash (LPA), or MgO plugging, results continually show the catalyst to be effectively cleared of chemical and physical deactivation substances, a decrease in pressure drop, increase in reaction surface, decrease in ammonia slip and increased plant efficiency.
Benefits
- Regeneration companies recommend this method be used to clean the catalyst before the modules are sent out for regeneration.
- It is the most effective method to prevent flyash release during highway transportation per EPA guidelines.
- Cleaning prevents moisture from accumulating in the plugged modules during transportation, which leads to hardening.
- It can reduce regeneration cost due to the prior cleaning.
- Turnkey comprehensive SCR cleaning incorporates vacuuming, proprietary sponge blasting process, module-encapsulation ash recovery & proprietary vibratory equipment and processes.
Applications
- Decrease in Pressure Drop
- Decrease in Ammonia Slip
- Reduced catalyst poisoning
- Cleared of chemical & physical deactivation substances
- Increase in Reaction Surface
- Increase in Plant Efficiency
- Reduced Risk of Boiler Shutdown